Exitex Utilises Customisation Toolkit to Get an Exact Fit for their Business
Exitex was established in 1981 by Brain C. Allport, with a factory in Mountpleasant, Carrickaneena, Dundalk, Co. Louth. The company was originally set up to design and manufacture a variety of weatherproofing products. Within 10 years, Exitex had established themselves as the leading Irish manufacturer of weatherproofing products for the construction and DIY sectors in both Ireland and the UK.
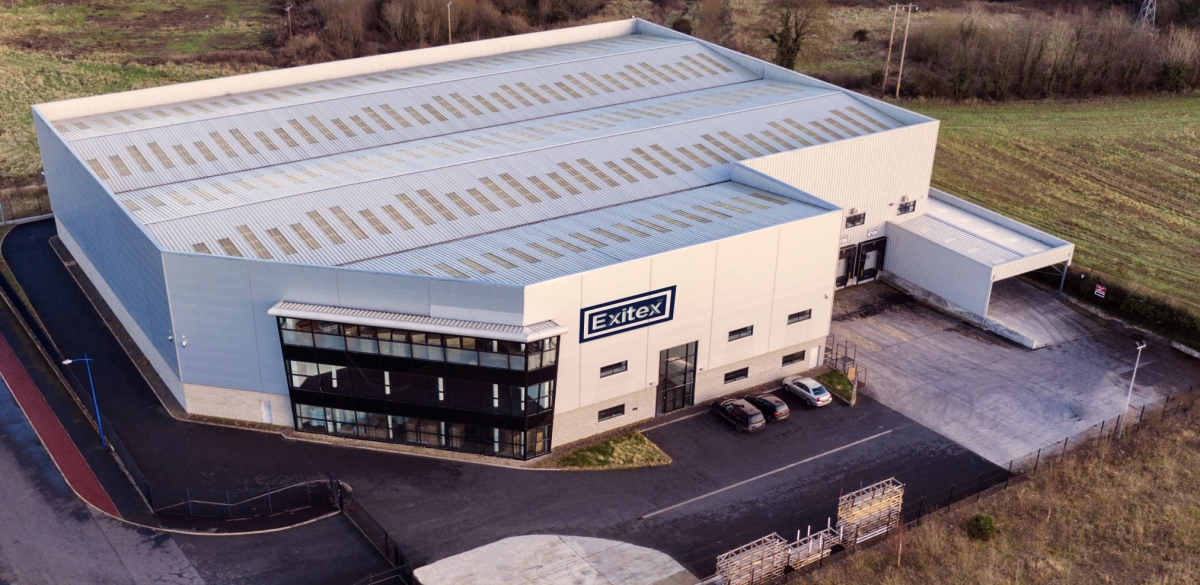
Customer Profile
Exitex was established in 1981 to develop a variety of weatherproofing products. By 1991, Exitex had established themselves as a leading Irish manufacturer of these products within the UK and Ireland.
The Challenge
Exitex were working on an outdated Sage 200 system. The current business system was unable to keep up with the needs of the business and there were limitations surrounding manufacturing and stock warehouse management.
The Solution
The EFACS system was chosen as it is an ERP system that is tailored to the manufacturing industry. EFACS is also highly configurable through the use of the Advanced Customisation Toolkit.
The Benefits
Exitex is no longer restricted by their business system. EFACS automates tasks, which has helped to manage an increased workload, while keeping staff levels the same. Paper documents, such as invoices, are easily scanned and held within EFACS.
In more recent years, Mr. Allport has stepped away from the business and it is now run by other family members. The business has been on an upward trajectory, including tripling the size of the Mountpleasant factory in 2003 to keep up with production demand. Furthermore, in 2012, a new distribution hub was acquired to help increase capacity, allowing the business to serve the ever changing needs of its customers. The company’s reputation has continued to grow over the years, with their products quickly becoming the standard within their respected markets within the UK, Ireland and wider Europe.
As a business, Exitex has seen tremendous growth since they opened in 1981. As the company continued to grow, they recognised that their business system, Sage 200, was unable to accommodate their expanding needs and there were a number of limitations, particularly around manufacturing and stock warehouse management.
It was decided that the business needed a new ERP system, one that would be able to aid the company in growth instead of holding it back. EFACS and Profitsflow were chosen for the project as the software provided the best fit for the business. Exitex also had previous experience of working with Tadhg Henderson, Managing Director at Profitsflow, before he founded Profitsflow. Ronan Treanor, Software Engineer, recalls that they knew “how customisable EFACS was compared with other ERP systems.” It was decided that the business would Go Live with the latest version of EFACS, which at the time was Version 8.5.
In preparation for Go Live of the software, a Profitsflow consultant delivering on-site training, particularly around the Customisation Toolkit and the Workflow tool within EFACS. The Customisation Toolkit was a great asset to Exitex, as it allowed them to configure the software to suit the business processes, without the need to change the underlying structure of EFACS. This also meant that Exitex were not locked into one particular version of the software, ensuring the system would be able to expand and change with the business’ needs.
Treanor explains that after the training with Profitsflow was conducted, “We established how the day to day business procedures could work in EFACS, we started working on reports & data transfer. We created over a hundred procedures to help synchronize data between both ERP systems”
Go Live was scheduled for November 2016. The company went Live with modules for Manufacturing, Scheduling, Suppliers, Customers, Workflow and Accounts. Treanor says, “As most of our modules are all interlinked, we had to Go Live across all departments in the factory”.
Exitex are a high transaction volume business. As such, the business has a high volume of paper based documents such as invoices to deal with on a daily and monthly basis. Before the implementation, one of the main challenges facing the business was how best to store and sort these documents. Treanor explains how EFACS helps to deal with the high volume of paperwork, “We scan our paper documents and use Workflow to store documents in the relevant area in EFACS. This has saved us countless hours looking in filing rooms.” By utilising the Document Management and Workflow tools in unison, the business is able to pass documents from one user to the next and recall document quickly and easily.
Profitsflow and Exitex continue to share a good working relationship and EFACS continues to support Exitex’s business processes. Looking to the future, Treanor adds, “All users have adapted to the change of the new version of EFACS. We are currently trying to set up routing on all products and implement electronic payments for suppliers. The extra features help us to improvement our service to customers and in turn will hopefully help us expand the business into the future”.
In conclusion, the successful implementation of the EFACS E/8 software by Exitex has led to a number of benefits, including the following:
- Customisation Toolkit allows for a precise fit for business processes
- Automate tasks via the Workflow tool
- Reduced the need for manual filing
- Integrated system including finance modules, such as Sales & Purchase Ledger
- Enhanced access to information for management decisions
- Less duplication of data