Chemifloc discovers the power of integration through EFACS E/8
Founded in 1982 Chemifloc Ltd. is a wholly Irish-owned bulk manufacturer of inorganic coagulants and a bulk chemical importer. Chemifloc offers a full rangeof water treatment chemicals to their clients. The company’s focus is on expanding its product portfolio, delivering unparalleled service to customers, and providing the best value for their investment.
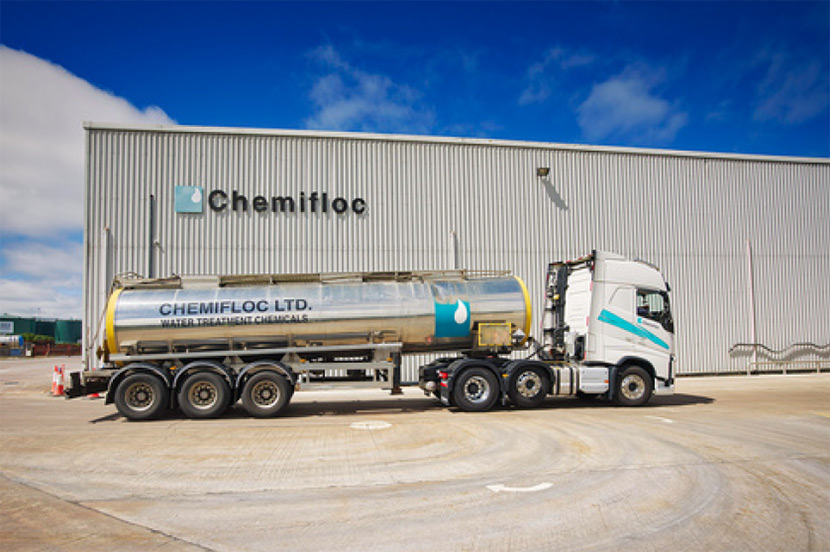
Customer Profile
Taking weeks to complete reports is now a thing of the past for Chemifloc as all the information needed from various systems can be extracted in a matter of days. EFACS has integrated seamlessly with Chemifloc which has allowed business operations to run through one single system.
The Challenge
Prior to meeting with Profitsflow, Chemifloc operated its business through the use of multiple separate systems. This meant the company had a significant duplication of work and labour intensive processes. As the company continued to grow it became evident that Chemifloc needed a single ERP system to provide a solution for all their requirements.
The Solution
True integration with EFACS E/8. An ERP system that gave the company a single information source that could provide real-time information from all departments.
The Benefits
Taking weeks to complete reports is now a thing of the past for Chemifloc as all the information needed from various systems can be extracted in a matter of days. EFACS has integrated seamlessly with Chemifloc which has allowed business operations to run through one single system.
The company was founded by business partners Hilary Lawless and Ed Storey and while both have since retired members of both families are still directly involved in the business.
The founders of Chemifloc both had backgrounds in chemical engineering, and they recognised the requirements of the multiple water treatment facilities throughout the island of Ireland. Since its foundation Chemifloc has always concentrated on service and quality for the customer. In 2002 it achieved the ISO9001 quality standard. The company has a team of highly experienced Technical Service Experts to provide backup and technical advice to the customer. This allows the customer to optimise the use of the recommended chemicals for their application. Our Technical Service people carry out Bench Scale Tests and Field Trials to solve customer problems. The wide range of products we supply ensures that the customers get the best cost performance solution for the application.
Originally supplying a handful of products to the market, the product range has grown to over a hundred, reflecting the ever-changing requirements in the water treatment industry.
Before implementing the EFACS E/8 ERP system, Chemifloc operated multiple separate systems to run the business which did not interact with each other. This resulted in significant duplication of work and labour-intensive processes.
As the company expanded, the Board of Chemifloc recognised the need for a single ERP system that would provide a solution for all their requirements. This was driven because of the fragmented way data was both stored and reported on. Because of the manual processes of transferring data this made it impossible to access information efficiently. Typically, monthly reporting would be three to four weeks after the month end.
Chemifloc first met Profitsflow at an ERP trade show and after looking at many different systems, EFACS E/8 was selected as the preferred ERP option. Chemifloc chose Profitsflow as its ERP partner because of their 25 years’ experience in implementing ERP systems and the flexibility of the EFACS software which allowed them to tailor the software to meet their unique needs.
Many of Chemifloc’s staff have been with the company for a very long time and because ERP software impacts all processes within the company, change management was recognised as a key element of the project. Previously all departments worked separately with little interaction. This silo approach and mentality was seen as a major blocker to the company’s growth. The experience and expertise of the Profitsflow project team helped greatly in leading the team through this process.
As EFACS was implemented during the Covid lockdown it led to unique training challenges. Chemifloc was still manufacturing as normal with office staff working on a hybrid model. This led to remote training which was scheduled on a weekly basis. This made preparation for go-live a little more challenging. Many of the core modules within EFACS such as Accounts, Material Management, & CRM were all implemented in Phase 1 and phase 2 will see the introduction of MRP, MPS and Capacity Planning.
The most immediate benefit Chemifloc has seen since go-live is that the whole business is now operating through one single system. From quotation to dispatch, all operations and documentation is held in EFACS. It is the single information source within the company providing real-time information on all aspects of the business. Gathering information for reports used to take weeks to complete due to the number of different systems. With EFACS these reports have been reduced to a matter of days.
As with any project of this magnitude, the go-live presented many challenges. The support and expertise of the whole Profitsflow team led to a smooth transition to EFACS. Their positive attitude to finding solutions to our unique requirements wwas both refreshing and well received by all the staff at Chemifloc.
A word from Martin Cahill, ERP Project Manager at Chemifloc:
“I expected a bedding in period after go-live of 5 ro 6 months and was amazed that within a month to six week everyone was seeing the benefits of EFACS.”